キャスティング(鋳造)について
ご存知のように、ものづくりには
① ものを削って加工する『切削』
② たたいて造形する『鍛造』
③ 溶かして型に入れ造形する『鋳造』
の3つの代表的な加工方法があります。
[toc]
鋳造とは
鋳造とは、金属を溶かして型に流し込んで成型する加工法の総称です。
鋳造にはいくつかの種類があります。古くは奈良の大仏などに代表される鋳造方法や、単純な形状であれば、耐熱材で作った合わせ型に溶湯を流し込む方法などもありますが、現代の一般的な工業生産では、『砂型鋳造』『ダイカスト』『ロストワックス鋳造』に大別できます。
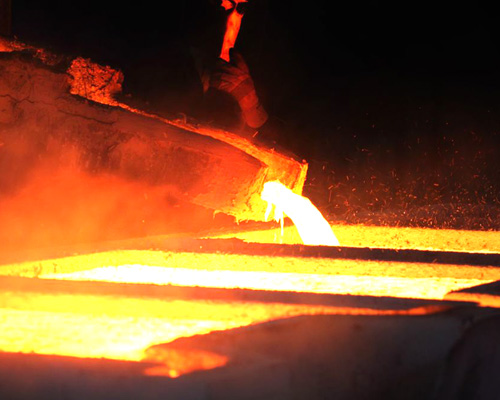
ロストワックス鋳造とは
ロストワックス鋳造技術は、古代エジプトで生まれ、日本には奈良時代に中国より伝わりました。
当時は、真土型鋳造(まねがたちゅうぞう)といわれる、灰と焼き土をまぜたもの(真土)を使って鋳造を行っていました。現在でも伝統工芸品では、金属の置物や壺などをつくる場合に、蜜蝋と真土型を組み合わせて鋳造が行われています。
例えば、金属の壺などをつくる場合、まず、縄を巻いて中子の芯をつくり、この表面に砥の粉で作った真土を塗り中子をつくります。この中子に蜜蝋を一定の厚みで塗るように張り、模様なども施します。
その後、再び真土を塗り、表面に真土を含んだ和紙を張ります。
これを850℃から900℃で加温して、中の蜜蝋を焼失させて空洞をつくり、これに溶湯を注ぎ入れて鋳造します。
これがロストワックス鋳造の原型とされる方法です。
ロストワックス鋳造は、タービングブレードなどの機械パーツ生産に代表されるセラミックシェル法(シェルモールド法)と、一般的には石膏鋳造とも呼ばれるブロックモールド法(ソリッド法)に分けられます。
ブロックモールド法は、歯科技工で個人に合わせた補綴物をつくる技術として広まりました。
また、ブロックモールド法を土台として、より精密な鋳造が行える方法として、従来の鋳型の製法とは異なるシェルモールドで鋳造を行うセラミックシェル法が開発されました。
シェルモールド法は、『第二次世界大戦中に、ドイツ人のヨハネス・クローニング博士により革新的な大量生産方法として発明されたシェルモールド法により軍事利用されはじめました。この鋳造法は1944年(昭和19年)にドイツで特許申請され受理されていますが、終戦後のドイツ特許は、連合国では特許として認めない公有物として、自由に工業利用が可能であったため、アメリカにおいて注目を浴び、急速に工業的発展を遂げた』とされています。(Being/AIによる回答)
日本には、戦後すぐにアメリカよりこの技術が伝わりはじめたようです。ブロックモールド法においても、同じころアメリカより技術とともに歯科技工用の鋳造機として日本に輸入され始めました。
1960年には、国産では初となる宝飾製品生産用の鋳造機として吉田キャスト研究所(現吉田キャスト工業株式会社)が開発・発売され、現在では「手作り」品以外では、ほとんどの宝飾品がロストワックス鋳造で生産されています(チェーンやコインなどは除く)。
セラミックシェル(シェルモールド)法とは
ロストワックス鋳造で、金型を使ってワックス型を射出成型するため、寸法精度で利点があり、ある程度大きな物も鋳造が可能な鋳造方法です。
ワックス型の回りにザーンカップで一定の粘度に調整されたセラミックとバインダーを混ぜたスラリーを塗り、その上から粒状のセラミックをまぶすように取り付けます(スタッコイング)。乾燥後に同じ工程を5日から7日にかけて、5回から7回続けて行い、5層から7層の殻(シェル)を重ねて鋳型をつくります。
一般的に、「ロストワックス精密鋳造」は、このセラミックシェル(シェルモールド)法を指します。
ブロックモールド(ソリッド)法とは
セラミックシェル法が発明される以前からあるロストワックス精密鋳造法です。
金型の代わりにゴム型にワックスを射出成型するため、寸法精度においてシェル法より劣りますが、ワックス型の取り出しの際の抜き勾配やアンダーカットの問題がないため、ワックス型の段階でのワークの形状やデザイン対して、あまり大きな制約がないところ、つまり自由度に利点があります。
ゴム製の円錐台(ゴム円錐台)の上にワックスツリーを組み立て、ステンリングと呼ばれる筒状の鋳型にいれて、水で溶いたブロックモールド法で使用する埋没材のスラリーを一次脱泡し、その後、脱泡済みのスラリーを鋳型に注ぎ入れ二次脱泡して、これを鋳型とします。
セラミックシェルとのちがい
セラミックシェル法は、ワックスを金型に圧入してワックス型をつくるので寸法精度面で利点があり、またある程度大きな鋳物も鋳造が可能などの利点があります。しかし一方では、金型作製の為のコストがかかり、鋳型作製で日数がかかります。
ブロックモールド法では、金型レスでワックス型の作製が可能で、鋳型づくりにかかる日数は約1日、これにより鋳造の生産コストが大幅に削減が可能となります。
また、シェルモールドをつくる場合、製品に「穴」や「突起が狭い間隔で並んでいる」形状の場合には、その穴の直径や突起の間隔が1cm以下の場合、充分な数の「シェルの層」ができないため型強度が不十分となり、形状の限界が存在します。
ブロックモールド法の製造ラインで必要となる装置導入のイニシャルコストはセラミックシェルと比べ、各段に低予算でラインの構築が可能です。
また、課題となる寸法精度でも、3Ⅾプリンターとの併用でセラミックシェル法と同等の寸法精度が得られます。
鋳造方案と金属
鋳造の方案(方式)には、大きく分けて4つの方法に大別できます。
詳しくはこちらページをご覧ください。
3Dプリンターとのコラボ
近年、PBF方式から派生した、いわゆる金属プリンター技術は日進月歩で進んでいます。しかしながら、「現状では形状による造型の限界」、「サポート除去」、「(一定以上の研磨が必要とされる場合の)造形表面の粗さ」、そして一時よりかなり価格は下がっているものの依然として装置導入の「イニシャルコスト及び消耗材料の価格が高額」などで、中小企業を含む全ての企業が導入できる状態ではありません。
ロストワックス鋳造の技法、とくにブロックモールド法は、3Dプリンター出力による造形物を金属に置き換えることが可能です。SLA方式・DLP方式・FDM方式(PLA樹脂)・一部のマルチジェット式の3Ⅾプリンターからの造形物をダイレクトキャスティングすることで金属3Ⅾプリンターを使わなくても3Ⅾプリンターの出力モデルを金属に置き換えることが可能です。
低予算でCADデータ(STL)を金属成型品に置き換えることができる、今いちばん現実的な技術です。
出力造形品の素材や置き換える金属により工程や設備が若干異なりますので、必要な設備などお気軽にご相談ください。